Recycled Polyester
An important fiber in our line, polyester allows us to build lightweight materials that dry quickly and can be used in a variety of applications, including creating our signature. Polyester also blends well with natural fabrics like cotton. But virgin polyester is derived from petroleum, which comes at a high environmental cost.
Recycled polyester, which has been available since the early 1990s, is now similarly priced to its virgin counterparts. Using recycled polyester reduces our reliance on petroleum as a source of raw materials, utilizes waste and reduces greenhouse gas emissions from manufacturing. Plus, by using recycled polyester, we can promote new recycling streams for polyester clothing that is no longer wearable.
Where we are?
We are committed to achieving RCS or GRS certification at 100% of our eligible fabric mills by 2025. When sourcing recycled materials, we ask our supply chain partners to be certified to approved third-party standards, including the Recycled Claim Standard (RCS) and Global Recycled Standard (GRS) certifications. These standards ensure robust chain of custody practices are in place and reduce the risks of unauthorized mixing or swapping of materials.
For the Fall 2023 season, 95% of our polyester fabrics by weight are made with recycled polyester.
What's next?
We’re looking to the next generation of potentially recyclable materials. Long-term, we’re also considering more chemical-recycling technologies that might allow us to reuse recycled garments and get us closer to a “circular” manufacturing process.
Made without PFCs / PFAS
Water repellency doesn’t just keep you comfortable, it keeps you alive. But for decades now, the coatings used in apparel to improve water-repellency have relied on per- or polyfluorinated chemicals, which contain fluorine and are most often referred to by their acronyms: PFCs, PFOAs or PFAS. This class of “forever chemicals” accumulates in air, water, food and even our bodies, and they raise serious health concerns, according to the Environmental Protection Agency.
What's the difference?
PFCs, PFAS, PFOS and PFOAs are different ways of conveying the same message: These acronyms refer to fluorinated chemicals with slightly different molecular structures and fairly similar functions. In the apparel industry, these acronyms are typically used interchangeably. At Patagonia, if your water-repellent finishes and membranes are made without PFCs, they’re also made without PFAS, PFOS and PFOAs.
Where we are?
From the beginning of BAXTER WOOD in Spring 2019, we launched our first products with DWR finishes made without PFCs while maintaining waterproofing.
Polyurethane
Polyurethanes are found in several of our products. They make up things such as our adhesives, waterproof and water-resistant coatings and films, spandex and foams. To avoid the use of PVC in our equipment and luggage lines due to its relatively high environmental impact, we have chosen to use polyurethane instead. The path to an eco-friendly polyurethane is much clearer and already underway. We are constantly striving to improve our manufacturing process and the materials that go into making our products in a way that’s better for the environment.
Where are we?
We use polyurethane. It’s found in waterproof products like the Trawler Coat and Longliner Coat. The stretch fibers and waterproof films we use are common, but we use them in different combinations than others in the industry in order to reduce our impact.
What's next?
Our goal is to use more recycled stretch yarns and bio-based polyurethanes in our products. This has the potential to reduce our CO2 emissions because these employ recycling processes that use former waste material (instead of virgin), and plant-based feedstocks.
What is vegetable tanning, exactly?
Chrome tanning stands as the most prevalent method of leather treatment in the global leather industry. Regrettably, the process involved in chrome tanning has significant environmental repercussions, particularly in developing nations. The hazardous wastewater generated during the tanning process can infiltrate the ground, causing detrimental effects on both soil quality and groundwater resources.
Where we are?
In contrast, vegetable tanning is an eco-friendlier alternative, relying on naturally derived tannins from tree bark, without any dependence on Chrome IV. At present, approximately 80% of our leather products are exclusively vegetable-tanned, while all our leather undergoes stringent testing, and the dyes we employ adhere to regulatory standards, devoid of any dangerous or banned chemicals, effectively eliminating the presence of chrome VI.
Nevertheless, this traditional method of vegetable tanning does have some drawbacks, including its substantial water consumption. Fortunately, these discharges do not pose environmental threats due to the use of organic materials. Nonetheless, the production cycle for a batch of vegetable-tanned leather extends to approximately two months, significantly longer than the one-day process for chrome-tanned leather. This extended duration, coupled with the need for skilled artisans and reduced automation, does contribute to a higher cost for this type of leather.
What is sustainable jewelry sourcing?
We craft jewelry with purpose — using sustainably sourced materials from certified factories that uphold the highest environmental and ethical standards. But our commitment doesn't end at creation. Through our jewelry registration program, customers can trace the journey of their piece and become part of a circular future. We invite customers to return their registered jewelry at any time for responsible recycling, giving old pieces new life while rewarding them with exclusive discounts toward their next meaningful purchase. Together, we're closing the loop and redefining what sustainable luxury means.
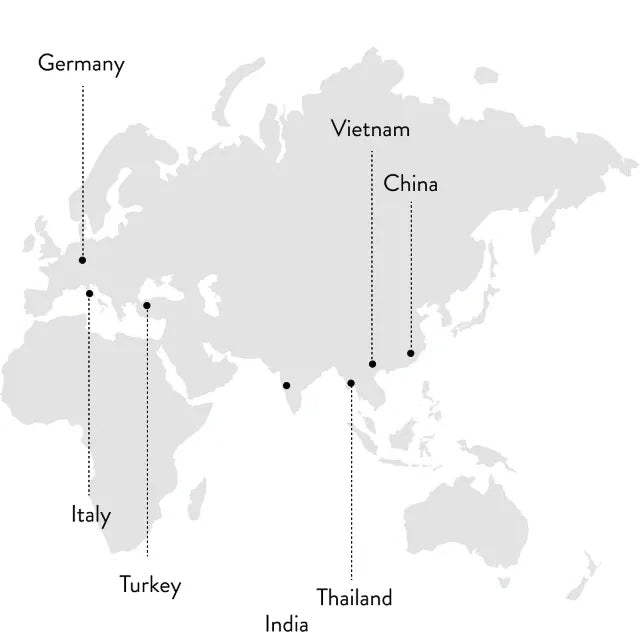